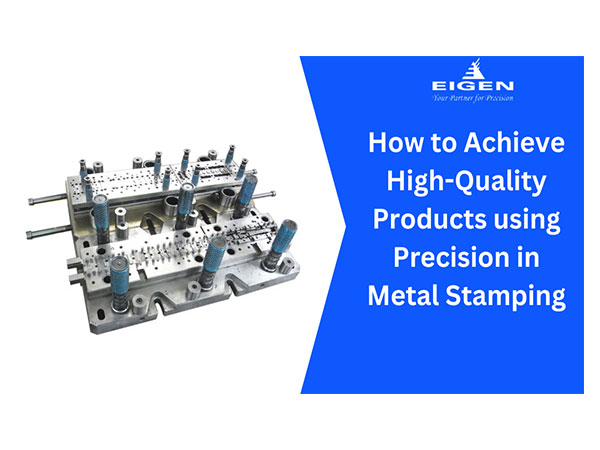
How to Achieve High-Quality Products Using Precision in Metal Stamping
May 08, 2024
VMPL
New Delhi [India], May 8: Metal stamping is a widely used production system that includes shaping steel sheets into preferred forms through the use of dies and punches. Precision in metal stamping is vital for producing top-notch merchandise with correct dimensions and nice finishes.
A precision stamping company employs skilled technicians who master the intricacies of excessive precision stamping to make sure the manufacturing of wonderful additives.
Here, let us discuss how to attain high-quality products using precision in metal stamping and give insights into achieving superior product pleasant via meticulous attention to detail.
Ensure the Correct Metal Stamping Design from the Onset
If engineers at metal stamping firms were granted one wish to boost process efficiency, it would be for manufacturers to engage them early in the part design phase.
Involving engineers from the outset ensures seamless collaboration, facilitating the alignment of design requirements with stamping capabilities, leading to more efficient and cost-effective metal stamping processes.
Anticipate Your Requirements
Transparency regarding anticipated requirements for the part and its final assembly, encompassing projected volumes and release frequency for the year, is imperative.
Engage in open communication with your stamper to discuss the potential ramifications of shipping frequency on overall costs.
By fostering transparency and collaboration, both parties can align their goals and strategies, leading to a more efficient and cost-effective metal stamping process that meets the specific needs and expectations of the project.
Evaluate Critical Tolerances in Metal Stamping
Tolerances in metal stampings, representing permissible variations from part specifications, can be a source of misunderstanding with manufacturers. Thoroughly assess these tolerances to avoid misunderstandings.
Customers choose a precision stamping company for their commitment to delivering precision stampings that meet the most demanding requirements in terms of accuracy and reliability.
Assess Dimensions for Final Assembly
When determining the appropriate dimensions for a part, it is vital to consider how it will fit into its final assembly. If the metal stamping needs to mate with another part or snap into place, these dimensions become critical.
Clearly assign accurate measurements to any critical dimensions on the drawing. To expedite time to market, the metal stamper may be designed and run in-die assemblies, eliminating unnecessary steps in the overall production process and reducing expenses.
Specify Accurate Production Volumes
Manufacturers may specify materials without fully understanding their behavior during the stamping process.
Metal stampers' engineers can assist in selecting the best material based on their knowledge of different materials' characteristics, tested during prototyping and simulation for performance validation.
Select Optimal Materials and Maximize Their Use
Manufacturers may request materials without understanding their behavior during stamping. With a focus on innovation, the precision stamping company continuously upgrades its precision tools to maintain its reputation for delivering precision stampings of the highest caliber.
Metal stamper engineers can assist in selecting the best material based on their knowledge, testing various materials during prototyping and simulation to validate performance.
Plan for Secondary Operations
Plan ahead for plating and other secondary operations, relying on the stamper for guidance and oversight. Schedule these operations to be handled as soon as possible after stamping to accelerate cycle time, with the metal stamping firm overseeing quality control.
High precision stamping requires cutting-edge technology and expertise, making the precision stamping company an industry leader in delivering exacting specifications.
Evaluate Simulations and Prototypes
Take advantage of a metal stamper's ability to provide 3D part simulations and prototypes to enhance manufacturability and reliability. Allocate time for tool design and development in the production schedule, ideally utilizing the stamper's in-house tool design and build capabilities.
Plan for Quality with APQP
A skilled steel stamper will adhere to the Advanced Product Quality Planning (APQP) process to ensure excellence from the outset.
As a leading precision stamping company, they make use of advanced precision tools to create complex and finely crafted stampings for various industries.
Monitor Quality in Real Time
To guarantee quality in metal stamping, employ statistical process control systems and in-die sensors for real-time tracking.
Evaluate the technology in place to ensure quality whilst assessing a metallic stamping supplier. Professional stampers use quality control methods to discover capability issues in real time, presenting manufacturers with quality reviews as needed.
Wrapping up
Precision in metal stamping is key to producing quality products with accuracy, consistency, and reliability. From accurate dimensions and tight tolerances to material control and quality inspection, each aspect of the stamping process should be meticulously controlled to acquire the desired precision stage.
(ADVERTORIAL DISCLAIMER: The above press release has been provided by VMPL. ANI will not be responsible in any way for the content of the same)